Many of the world’s potential reserves of hydrocarbons lie beneath the sea, and the hydrocarbon industry has developed techniques suited to conditions found in the offshore, both to find oil and gas and to successfully produce it.
Modern and advanced drilling techniques and methods have increased Companies’ ability to find hydrocarbons and the speed at which their projects are developed.
There are technology advances for exploration and development, better control of environmental impacts, increased efficiency, and improved understanding of the marine environment.
The techniques and equipment for drilling offshore wells (offshore drilling) are very similar to those used for onshore drilling.
The main differences consist in the arrangement of the drilling rig and of the equipment, and in certain particular methods of carrying out the operations, which have to be adapted to the requirements dictated by far more difficult and often extreme environmental conditions.
This entails considerably higher costs, to which must also be added considerable investments to provide the facilities and plants for subsequent field development.
An offshore drilling rig has to create the same working conditions as for onshore rigs which can move from one point to another without any difficulty, and they have several additional features to adapt them to the marine environment, including:
- Heliport
- a large deck area that is placed high and to the side of offshore rigs;
- It is an important feature since helicopters are often the primary means of transportation.
- Living quarters
- usually comprise bedrooms, a dining hall, a recreation room, office space, and an infirmary.
- Cranes
- used to move equipment and material from work boats onto the rig and to shift the loads around on the rig.
- Risers
- used to extend the wellhead from the mudline to the surface.
These conditions increase the complexity of the offshore rigs, and justify their higher daily rate compared with an onshore drilling rig of the same capacity.
From an operational point of view, offshore drilling may be subdivided into two main categories, depending on the water depth.
- Bottom supported drilling rigs
- The safety equipment, i.e. ordinary Blow-Out Preventers (BOPs) located permanently above sea level and accessible from the supporting structure;
- drilling operations are identical to those carried out in onshore drilling.
- Floating drilling rigs
- The wellhead and the subsea BOPs are placed on the seabed, and are not therefore directly accessible from the supporting structure.
- Drilling operations differ from onshore ones, as the rig floats, subjected to the action of the wind, currents and waves, which cause it to make small horizontal and vertical movements.
- The use of floating rigs is necessary for exploratory drilling in water depths of more than 100 m (this refers solely to exploratory drilling operations, and not to the subsequent development drilling).
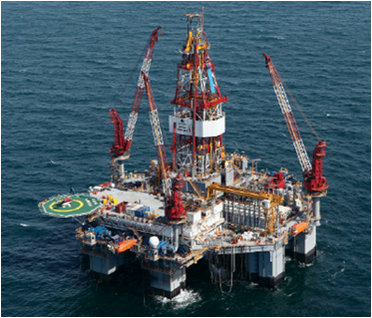
Exploration Drilling Rigs (from Shell)
Bottom supported rigs
- Barges
- They are designed to work in shallow water (less than20 ft deep).
- The rig is floated to the drillsite, and the lower hull is sunk to rest on the sea bottom.
- The large surface area of the lower hull keeps the rig from sinking into the soft mud and provides a stable drilling platform.
Drilling Barge (from Parker Drilling)
- Submersibles
- They are barge that are designed to work in deeper water (to 50 ft deep);
- They have extensions that allow it to raise its upper hull above the water level.
Submersible Drilling Rig
- Platforms
- Platformsuse a jacket (a steel tubular framework anchored to the ocean bottom) to support the surface production equipment, living quarters, and drilling rig.
- Multipledirectional wells are drilled from the platform by using a rig with a movable substructure.
- The rig is positioned over preset wellheads by jacking across on skid beams.
- After all the wells are drilled, the rig and quarters are removed from the platform.
- Smaller platforms use a jackup rig to drill the wells.

Offshore Drilling Platform
- Jackups
- Jackupsare similar to platforms except that the support legs are not permanently attached to the seafloor – The weight of the rig is sufficient to keep it on location
- The rig’s legs can be jacked down to drill and jacked up to move to a new location – when under tow, afloating hull buoys the jackup.
- Thederrick is cantilevered over the rear to fit over preset risers if necessary.
Jack Up Drilling Rig
Floating drilling rigs
- They are not attached or resting on the ocean bottom and have special features to facilitate this:
- They are held on location by anchors ordynamic positioning
- Thedrill string and riser are isolated from wave motion by motion compensators.
There are two categories of drilling floating rigs
- Semi-submersible rigs
- They consist of a large triangular, rectangular or pentangular platform, connected with submerged hulls by means of large columns which vary in number from 3 to 8, according to the shape of the vessel
- They are kept vertical over the site by means of mooring or dynamic positioning systems
- Semis are subjected to wave motion, their drilling apparatus is located in the center where wave motion is minimal.
- Semis are flooded to a drilling draft where the lower pontoons are below the active wave base, thereby stabilizing the motion.
Semi Submersible Drilling Rig
- Drill ships
- Drilling ships are used for operating in deep waters, often under extreme environmental conditions, such as drilling in arctic areas
- Drilling ships represents on optimal solution of drilling exploratory wells in remote areas, far removed from supply points, as it can carry all the material necessary for drilling even a particularly difficult well.
- Drilling ships are kept in a vertical position over the well by means of mooring or dynamic positioning systems
- Drilling ships when moored can be used for drilling in depths of up to about 1,000 m, while for greater depths dynamic positioning systems must be used, and with these the ship is capable of operating in 3,000 m of water
- The drilling apparatus on a drill ship is mounted in the center of the ship over a moon pool, which is a reinforced hole in the bottom of the ship through which the drill string is raised and lowered
- The ship can be turned into the oncoming wind or currents for better stability
Drilling Ship (from Maersk Drilling)
Drilling from floating offshore rigs
The techniques for drilling offshore wells from floating rigs are basically the same as those used for onshore wells.
In general, the factors involved in drilling wells from floating rigs are due to the following:
- the wellhead is located on the seabed;
- the submarine BOPs are located on the subsea wellhead and are controlled hydraulically or electrically from the surface;
- the BOPs are connected to the rig by means of a marine riser(enabling the drilling fluid to circulate upwards);
- the marine riser, connected at the top of the BOP stack, has a ball joint on its base and a slip joint above sea level to offset the horizontal and vertical movements of the rig;
- the lines for preventing blowouts (kill lines and choke lines) run from the surface manifold on the rig to the subsea wellhead, as independent lines fixed to the outside of the marine riser.
Offshore drilling operations
Drilling starts after the rig has been positioned vertically over the well, by means of mooring or dynamic positioning systems.
- The first operation consists in placing on the seabed (by means of a pipe string) of a temporary guide base( a strong steel framework with a central hole which has a tapered inlet at the top, provided with four guidelines and a number of steel pins that become embedded in the seabed and prevent displacement).
- The pipe string is then disconnected, leaving only the temporary guide base on the seabed, with the four guidelines that connect up with the rig.
- Now, the drilling phase can begin, so as to place the first casing (the foundation pile) and it is carried out using the circulation of seawater, the cuttings do not rise to the surface but are scattered over the seabed.
- The foundation pile is taken down to a depth of a few tens of metres.
- At this point the foundation pile is lowered into the hole again using a light frame and the four guidelines.
- The foundation pile ends with a permanent guide structure, characterized by four tubular columns placed at the apexes, through which run the guidelines.
- The four columns serve in the subsequent phases to guide the submarine BOPs to the wellhead with precision.
- The permanent guide structure contains the housing for the wellhead, to which the successive casings will be anchored.
- The subsea wellhead has a different system of flanging and anchoring the casings and it is shaped in such a way as to enable the lock-up of the hydraulic connector to which the BOPs are coupled.
- Next, the foundation pile is fully cemented by means of a drill string.
- Once the cement has set, drilling continues, boring the second section of the hole inside the foundation pile, in which the second casing is inserted.
- Once the conductor pipe has also been fully cemented, the well has a stable structure and it is possible to install the submarine BOPs.
- After this drilling continues with the sequence of operations typical of onshore wells.
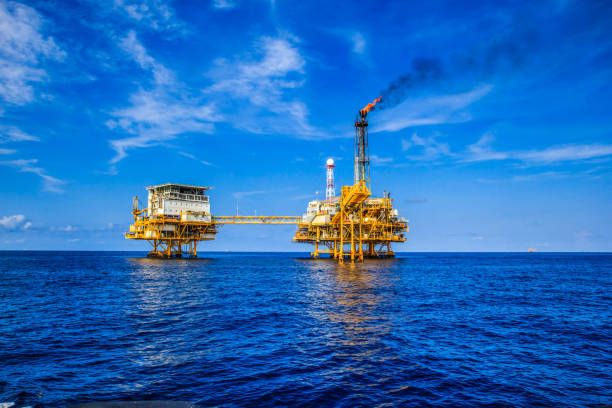
Drilling from floating vessels (from Encyplopaedia of Hydrocarbons ENI)
Subsea BOPs
In offshore drilling BOPs have the same function as those used in onshore wells, but are connected in a single complex (the BOP stack) before being mounted on the wellhead, so as to reduce assembly times at the sea bottom.
They are lodged in a square-section cage structure with female columns at the apexes, into which the male tubular columns of the permanent guide structure fit.
The BOP stack is lowered and fastened to the wellhead by means of a hydraulically controlled connection, ensuring hydraulic sealing.
In the event of temporarily abandoning the well because of adverse weather and sea conditions, it is possible to suspend the pipes on the shaped rams of the lower BOP, to unscrew the pipes and to close the well with the upper blind rams – at this point it is possible to disconnect also the marine riser and possibly to abandon the site.
The marine riser can be reconnected when the sea and weather conditions improve.
The hydraulic lines controlling the various functions of the BOP stack converge in a connector block, to which is connected the bundle of flexible pipes for their control from the surface.
The BOPs can be operated in a similar way to that used in onshore wells, known as the direct system.